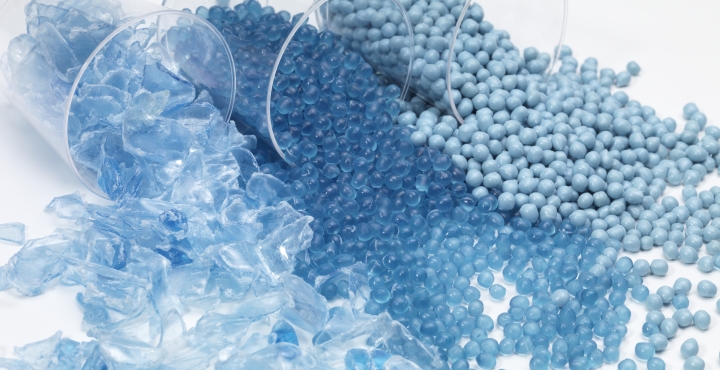
APET Levha Hattında Geri Dönüşüm Malzeme Kullanımı
Hidroskopik bir malzeme olan PET içinde kalan nem proses sırasında degredasyona neden olarak hem folyonun ve hem de bir sonraki adım olan termoform sonrası ürünlerin bozulmasına yol açacaktır. APET granül ve kırma malzemeyi kuruturken aşağıdaki ipuçlarını takip ederek nemi prosesinizden uzak tutabilirsiniz.
Levha ve folyo ekstrüzyonunda kullanılan PET (amorf PET genellikle APET olarak gösterilir), enjeksiyon için kullanılan polimerin hemen hemen aynısıdır. Şişirmede karşılaşılmayan bazı sorunları ortadan kaldırmak için bir miktar modifiye edilmiş olabilir ve içsel viskozitesi (IV) daha düşük olabilir, ancak esasen aynı malzemedir.
APET, sağladığı şeffaflık, optik netlik, parlaklık, yüksek mukavemet, düşük maliyet ve gıda paketlemeye uygun kimyasal yapısıyla paketlenmiş ürünlerin teşhirini optimize eden ve böylece mağaza rafında çekici bir görünüm sağlayan ideal bir malzemedir.
Ulaşılabilirliğine rağmen, PET son ürünün istenen özellikleri elde etmesi için üreticilerin üstesinden gelmesi gereken birkaç zorluk ortaya koymaktadır. Bu zorlukların başında da nemin uzaklaştırılması geliyor. PET higroskopiktir; bir denge durumuna ulaşılana kadar atmosferden nemi hızla emer, bu nem ekstrüzyon sırasında ayrışarak hidrolitik bozunmaya sebep olacağından işlem sırasında veya öncesinde malzemeden atılması gerekecektir. Bir süre öncesine kadar nemi uzaklaştırmanın tek yolu kurutma idi, günümüz teknolojisinde ekstrüzyon sırasında ventilasyonla nemin atılması da mümkün.
Malzeme tedarikçileri tarafından belirlenen APET için kurutma gereksinimleri, diğer herhangi bir PET uygulaması için verilenlerle aynıdır. Üreticinin tavsiyelerine bağlı olarak, kurutma sıcaklıkları 4 ila 8 saat boyunca 150°C ila 175°C aralığında ve kurutma havasının çiğ noktası -30/-40°C aralığında olmalıdır. Kabul edilebilir nihai nem miktarı çoğunlukla malzeme tedarikçileri tarafından belirtilen, 30 ila 50ppm (%0,003 ila %0,005) aralığında veya daha düşüktür.
Paketleme sınıfı PET tedarikçilerinin çoğu, iyi optik netlik ve parlaklık ile birlikte yavaş kristalleşme hızı gibi APET levha uygulamaları için gelişmiş özellikler sağlamak üzere özel olarak formüle edilmiş bir malzeme kalitesi sunar. Kullanılan virgin granüller 0.70 ila 0.84 IV değerine sahiptir ve süt beyazı rengindedir yani kristalizedir. 175°C 'ye kadar sıcaklıklarda "olduğu gibi" kurutulabilir. Malzeme nakliye ve depolama sırasında atmosfere maruz kaldığında nemi emecektir ve bu nedenle nemin tekrar uzaklaştırılması gerekecektir. Şekil-1, 175°C'de kurutulduğunda kristalize PET için nem kaybı eğrisini gösteren tipik bir kurutma analizi grafiğini gösterir.
Hurda Malzeme İle Yaşanan Zorluklar
APET levha ekstrüzyonunda kenar trimleri ve termoforming prosesindeki kesimden kalan iskelet nedeniyle ciddi miktarlarda hurda malzeme artmaktadır. Özellikle termoformda üretilen ürünler kare veya dikdörtgen ise, ürünler arasındaki hurda alanı aza indirilebilir ancak ürünler yuvarlak, oval veya birbiriyle iç içe yapılamayacak düzensiz şekillere sahipse, kesim alanı artacaktır ve bu nedenle hurda oranı, toplam ekstrüder kapasitesinin %50'sini kolaylıkla aşabilir. Bunun yanında minimum standartları kaşılamayan levha rulolarından da ciddi miktarda hurda dönüşleri olabilir.
Birçok APET levha ekstrüzyon üreticisi, ticari nedenlerle dış kaynaklardan geri dönüştürülmüş PET kırma satın alır. Malzemenin geçmişine yani ana kaynağına bağlı olarak özel yıkama ve arıtma önlemleri gerektirebilir. Mesela ilaç sanayiinden elde edilen PET malzeme ile, belediyelerin geri toplama tesislerinden alınan malzeme veya kontrolsüz şekilde atık noktalarından toplanan yani kullanım alanı tek tip olmayan malzeme farklı yıkama tekniklerine tabi tutulabilir.
Şirket içinde üretilen kırmanın yeniden kullanılmasıyla ilgili olarak ele alınması gereken çeşitli zorluklar vardır, örneğin:
1. APET kırmanın taşınma ve akış özellikleri.
2. APET ürünlerin kırılması sırasında ortaya çıkan ince çapak.
3. APET kırmanın zayıf kütlesel akış özellikleri.
4. APET kırmanın tekrar 50ppm altına kurutulmasıyla oluşacak komplikasyonlar.
APET kırma malzemenin düzensiz boyutu, şekli ve düşük kütle yoğunluğu taşınmasını zorlaştırır. Ayrıca APET kırma malzeme düzdür ve silolarda depolandığında yapışma eğilimi gösterir. Malzeme silodan iletim sistemi borusuna geçerken, yapışma eğilimi dolayısıyla köprüleme yapabilir ve bu malzeme akışında kesintilere neden olur, hatta tamamen tıkayabilir. İletim hattına daha iyi malzeme akışı sağlamak için toplama borusunun açılması, genellikle iletim hattının aşırı dolmasına ve taşmasına neden olur, bu da iletim sistemde akış düzensizliği yaratır.
Kırma malzemenin akış özelliklerini iyileştirmek ve köprülemeyi önlemek için kullanılabilecek bir yöntem, kırmayı daha küçük bir parçacık boyutuna parçalamaktır. 3/8-inçlik veya daha büyük bir elek kullanmak yerine, daha küçük ölçülü (5/16 inç) bir elek kullanılabilir. Bu, kırmanın hem taşıma özelliklerini iyileştirecek hem de kütle yoğunluğunu arttıracaktır. Ancak olumsuz yanı, üretilen ince tane yani çapak miktarını da artırmasıdır.
Malzemenin kurutucu hunisinden geçerken kuruma süresinin kontrol edilmesi için malzemenin kütle akışının sağlanması şarttır . Kırma malzemenin geniş düz yüzey alanı ve düşük kütle yoğunluğu, kurutma hunisinin içinde zorlanan karşı hava akışı ile birleştiğinde, malzemenin düzenli olarak aşağı doğru akışına negatif etki edebilir.
Kurutucu havanın, kurutma hunisinden geçen malzeme akışına müdahale etmesini önlemek için yapılabilecek birkaç şey vardır. İlk olarak, pulun parçacık boyutunu yukarıda açıklandığı gibi küçültülmesi. Başka bir yöntem, kurutma hunisinden geçen kurutma havasının hacmini, malzeme çıktı miktarına uyacak şekilde ayarlamaktır. Aşırı hava akışı, yalnızca kurutma hunisinden geçen malzemenin akışını bozmakla kalmayacak, aynı zamanda malzemeyi kurutmak için gerekenden daha fazla miktarda enerji tüketecektir.
APET yarı mamül ve ürünler geri dönüşüm için kırılırken büyük miktarlarda ince çapak ve talaş oluşur – bu prosesin doğasıdır. Kırıcı bıçaklarının keskinliği ve bıçak boşluğu, bu küçük taneciklerin ortaya çıkmasındaki kritik noktalardır. Bu pratikte zor olsa da bıçak keskinliği her zaman korunmalıdır ve bıçaklar arasındaki boşluk, kırıcının malzemeyi toz haline getirmek yerine kesmesini sağlamak için minimumda tutulmalıdır.
Levha üreticileri bazı uygulamalarda kırıcıdan çıkan malzemeyi doğrudan kırıcının çıkışına bağlı bir havalı konveyör ile tahliye eder. Bu blower, pulları kırıcının çıkışından çeker ve bir çark vasıtasıyla hedefine üfler. Üfleyicinin çarkı daha fazla miktarda talaş oluşturacağından, bu tip taşıma PET ile iyi bir uygulama değildir. Vakumlu bir taşıma sistemi, kırıcıdan nihai varış noktasına kadar taşıma hızını kontrol etmek için araçlar sağlar ve onu oldukça düşük bir hızda (pulun toplanma hızının hemen üzerinde) tutar, bu da ince taneciklerin ve yılan derisi efektinin oluşumunu azaltacaktır.
PET'in yüksek sıcaklıklarda kurutulması, işlemeden önce 50 ppm veya daha düşük düşük nihai nem seviyesine ulaşmak için ön koşuldur. Bu sıcaklık aralığı, tipik olarak 230°C'nin üzerinde olan erime sıcaklığına yakın bir sıcaklığa ısıtılana kadar yumuşamaya başlamayan kristalize PET (granül veya pul) kurutulurken bir sorun oluşturmaz.
Bununla birlikte, kurutulmuş kristalize PET ekstrüdere girdiğinde polimer içindeki kristalin yapı bozulacak ve polimer berrak, şeffaf, amorf duruma geri dönecektir. Ekstrüderden çıkan levha hızla soğutulur ve amorf halde dondurulur. APET levha kenar triminden ve ağ iskeletinden çıkan malzemenin yeniden kullanılmasındaki en büyük zorluk, onu kurutmaktır.
Amorf PET kırması ısıtıldığında kristalize PET'ten farklı tepki verir. Amorf PET, bileşimine bağlı olarak (75-90°C) genellikle 82°C'de başlayan bir cam geçiş sıcaklığına sahiptir. Camsı geçiş sıcaklığına kadar ısıtıldığında yumuşamaya, kaynamaya ve topaklaşmaya başlayacak, bu da kurutma hunisinde akışın durmasına neden olacaktır. Bu nedenle, kurutma hunisinde aglomerasyonu önlemek için amorf kırma, yüksek sıcaklıkta kurutmadan önce kristalleştirilmelidir.
Kristalize PET Flake (Pul)
Kristalleştirme, PET'in camsı geçiş sıcaklığının üzerinde bir seviyeye ısıtılmasıyla gerçekleştirilir. Kristalleşme sıcaklığı ne kadar yüksek olursa, amorf pul o kadar hızlı kristalleşir. Pul kristalleştirilirken, topaklaşmasını önlemek için agresif bir şekilde çalkalanmalıdır. Pul, amorf halden kristal duruma geçerken, polimer içindeki kristal oluşumundan dolayı berrak, şeffaf bir puldan süt beyazına dönüşecektir. Kristalleşme sırasında pulun yüzeyi sertleşir ve erime sıcaklığına kadar ısıtılana kadar tekrar yumuşamaz.
PET flake kristalleştikten sonra 50 ppm veya daha düşük düşük nihai nem seviyelerini elde etmek için gereken yüksek sıcaklıklarda kurutulabilir. Şekil 2, 150°C'de kurutulduğunda kristalli PET pulu için nem kaybı eğrisini gösteren tipik bir kurutma analiz grafiğidir. Kristal pulun düşük başlangıç nem içeriğine dikkat edin; bunun nedeni pulun sıcak (175°C) ortam havası ile kristalleştirilmesidir, bu da sınırlı bir kurutma sağlar ve işleme için gereken düşük nem seviyelerini elde etmek için yeterli değildir.
APET pulunu kristalize etmek için gereken ekipman maliyetlidir ve tesis içinde değerli yer kaplar, bu da bazı işlemcileri işlemeden önce pulu daha düşük sıcaklıklarda (65C) kurutmayı denemeye zorlamıştır. Ne yazık ki, PET'in cam geçiş sıcaklığının altındaki bir kurutma sıcaklığında 50 ppm veya daha düşük düşük nihai nem seviyesine kadar PET'in kurutulması hiçbir koşulda mümkün değildir.
Bu şekilde kurutulan PET'in ekstrüde edilmesi, bir miktar hidrolitik bozunma, daha düşük IV ve ekstrüde edilmiş tabakanın optimal olmayan fiziksel özellikleri ile sonuçlanacaktır. 50 ppm veya daha düşük bir son nem seviyesine ve sağladığı faydalara ulaşmak istiyorsanız, önce kristalleştirmeniz ve ardından önerilen sıcaklıklarda kurutmanız gerekir. Şekil 3, amorf PET pulunun 65C'de kurutulmasının zayıf performansını gösteren bir kurutma analizi grafiğidir.
APET pulunu yeniden kristalleştirmeden işlemede bir miktar başarı elde etmiş olan APET levha ekstrüderleri, bu başarıyı, ürettikleri ürünün fiziksel gereksinimlerinin diğer birçok APET ürünü kadar talepkar olmaması gerçeğine bağlayabilir. Buna ek olarak, büyük olasılıkla, ortamdaki hava koşullarıyla birlikte gelen ve giden bazı kalite sorunları yaşarlar. Ortam neminin düşük olduğu soğuk kış ayları en sorunsuz aylarıdır.
İşleme ve kalite sorunlarının çoğu, haziran, temmuz ve ağustos aylarının sıcak ve nemli yaz aylarında ortaya çıkar. Soğuk ve kuru kış ile sıcak ve nemli yaz arasındaki süre, çoğunlukla hava koşullarına bağlı olarak iyi veya kötü olabilir.
PET ekstrüzyon teknolojisi hakkında daha fazla bilgi için bizimle irtibata geçin !
Kaynaklar: How to Keep Moisture Away From Your APET Sheet Line - Pete Stoughton.