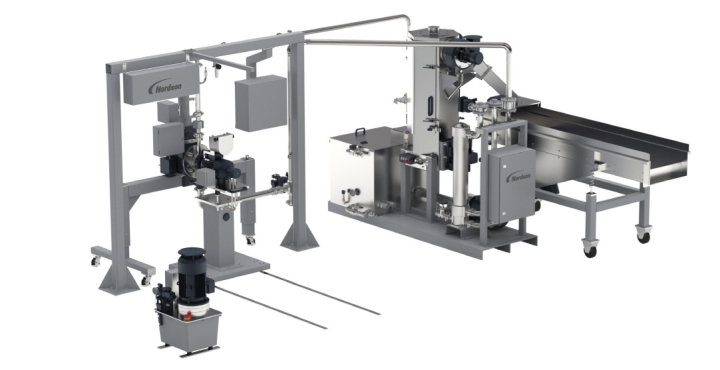
Doğru Pelletizer Sistemini Seçmek
Uygulamanız için hangi pelletizer sistemi doğru? Hangisi daha efektif? Bugün kullandığınız, yarın için mutlaka doğru seçim mi? İşinizi çeşitlendirmek istediğinizde elinizdeki sistem size yeterli olacak mı? İşte üç ana seçenek arasında karar vermenize yardımcı olabilecek bir çalışma sizi bekliyor…
#pelletizer #peletleyici #compounding #recycling #polimerization #geridönüşüm #UWP #WRP #strand
Pelletizer yatırımı yapmayı planlayan şirketler, temel maliyet değerlendirmesine ek olarak operasyonel ve uygulama ihtiyaçlarının kapsamlı bir envanterini yaparak doğru sistemi seçebilirler. Her biri belirgin şekilde farklı güçlü ve zayıf yönlere sahip üç ana tip pelletizer sistemi mevcuttur. Plastik endüstrisinin büyümesi ve pazarda sürekli olarak yeni gereksinimlerin ortaya çıkmasıyla birlikte, belirli bir sistemi uzun süredir kullanan bir şirketin bile kapasite ekleme zamanı geldiğinde bir alternatifi düşünmesi gerekebilir.
Pelletizer hatları polimer üretimi, compound oluşturma, masterbatch üretimi ve geri dönüşümde kullanılacak primer makinelerdir. Bir polimerizasyon tesisi için uygun olan yüksek hacimli bir pelletizer sistemi ile bir özel reçete compound üreticisinin kullandığı sistem, masterbatch te kullanılan bir sistem ile postconsumer geri dönüşüm hattı birbirinden çok farklı gereksinimlere sahip olacaktır. Aşağıda her türün bir değerlendirmesi yer almaktadır.
SU ALTI KESİM HATTI
Sualtı kesim hattı (UWP), kalıp yüzü temaslı bir pelletleyicidir. Bu, erimiş polimerin yuvarlak bir kalıpta dairesel şekilde 1-2-3 sıra olarak dizilmiş olan deliklerden makarna halinde çıkarken kalıp yüzeyinde sürekli ve hızla dönen bir dizi bıçak tarafından sürekli kesilmesi ile çalışır. Su halkalı (WRP) pelletizerden en önemli farkı, kesme odasının tamamen basınçlı proses suyuyla dolu olmasıdır. Yani eriyik kalıptan direkt olarak suyun içine çıkar ve suyun içinde kesilir. Yüzey gerilimini en aza indiren kuvvetler nedeniyle, her bir granül UWP'lere özgü küreye en yakın şekli alır ki bu şekil granül malzemenin kuru akış karakteri açısından en istenen durumdur.
Sürekli çevrim halinde olan kapalı devre proses suyu, kesilen granülleri kesme odasından bir aglomer yakalayıcıya (yapışmış plastik topaklarını yakalar ve ayırır) ve ardından bir santrifüjlü kurutucuya taşır. Kurutucunun alt girişinde granüller sudan ayrılır, kaldırma kanatlı döner bir şaft yardmı ile kurutucunun üstüne doğru yol alırken hem sıcak hava hem de santrafüj etkisi ile granüller kurutulur. Burada kullanlan kurutucu temelde su halkalı pelletizerde kuulanılanla aynıdır.
Diğer pelletizer sistemlerinde olduğu gibi, UWP'deki kurutucu, bir taraftan sıcaklığını kontrol edip sabit bir aralıkta tutan (gerektiğinde ısıtıp gerektiğinde soğutan), diğer taraftan da kesim sırasında ortaya çıkan ve suyun içinde bulunan polimer tozu ve ince taneleri filtreleyen iki yardımcı sistem ile donatılmıştır. Su sıcaklığı dar bir aralıkta kontrol edilir ve kesilen polimerin özelliklerine göre ayarlanır. Yani eriyiğin kalıptan çıkış sıcaklığı, ilk teması sağladığı suyun sıcaklığı, suyun hızı, alınacak yolun süresi, bu süre boyunca yapılacak ısı transferi, sonucunda kurutucuya girmeden önce pelletin düşeceği sıcaklık, hepsi kontrol altındadır. Bunun yapılmaması, hatalı biçimlendirilmiş peletlere, zayıf fiziksel özelliklere veya proses kesintilerine neden olabilir.
UWP'lerde, tüm soğutma suyu, diğer pelletizer sistemlerinden farklı olarak kesici ve kurutucu arasında kapalı bir sistemde borular vasıtasıyla taşındığı için kesici ve kurutucu birbirinden bağımsız yerlere konumlandırılabilir. Kurutucu ve alt ekipmanları, kesiciden belirli bir mesafeye, örneğin başka bir odaya veya başka bir zemine kurulabilir. Bu da kullanıcıya bir yerleştirme esnekliği sağlar.
Su borularının mümkün kıldığı bir diğer özellik, suyun kesme odasından akışını değiştirirken gerekli sıcaklığı korumak için devridaim etmesine izin veren su baypas sistemidir. Bu, operatörün kesici kafayı değiştirmek gibi görevleri gerçekleştirmek için pelletizeryi kesme odasından ayırmasını sağlar.
Kapalı devrede bulunan bir baypas sistemi, kalıp deliklerine polimer akışını durdurmak ve başlatmak için kullanılan bir polimer yön değiştirme valfi ile koordineli olarak çalışır. Bu ikili sistem sayesinde ilk çalıştırma esnasında ekstrüder içinde kalan partiküller temizlenebilir, kalıp delikleri temizlenebilir, kesici haznesi temizlenebilir, güvenli bir şekilde start verilebilir veya üretimin herhangi bir anında bıçak takımı değiştirebilir. Tüm süreç otomatik olarak yönetilir, çok kısa sürelerde gerçekleşir..
Kesme bıçaklarının kalıp plakası üstündeki basıncını kontrol etmek için çeşitli seçenekler mevcuttur. Bunlar arasında operatörün basit bir çıkrık kullandığı manuel sistemden PLC kontrollü hidrolik loadcell e kadar birkaç alternatif bulunmaktadır. Bu şekilde kalıp ve bıçak arasındaki boşluk kontrol edilebilir. Bu değer kesme kalitesi ve aşınma süresi üzerinde belirleyicidir.
Proses suyunu temizlemek için de değişik sistemler mevcuttur. Giriş seviyesi kaset tipi bir sistem, 2.000 kg/saate kadar kapasiteye sahiptir ve 150 µ'a kadar olan ince parçacıkların sürekli otomatik filtrasyonu için isteğe bağlı bir bant filtre ile seviyesi yükseltilebilir. Daha ayrıntılı sistemler, otomatik olarak kendi kendini temizleyebilen, 70 µ'a kadar filtreleme sağlayan ve 35.000 kg/saat kadar büyük kapasitelere sahip olan filtreler de vardır.
Yukarıdaki özelliklerin gösterdiği gibi, UWP en karmaşık pelletizer sistemidir ve en büyük yatırım bütçesini gerektirir. Buna karşılık, bu alanlarda diğer pelletizer sistemlerine göre bariz birtakım avantajlar sunar:
● Otomasyon. UWP, birçok özelliğini yöneten PLC kontrolü ile otomasyon için en geniş kapsama sahiptir. Bıçak bileme ve hat içi kalıp plakası taşlama gibi işlevler önceden programlanabilir, bu da duruş süresini en aza indirir.
● Kontrol edilebilirlik. UWP'ler, diğer pelletizerlere göre onlarca daha fazla kontrol parmetresine sahiptir. Ve bu kontrol kabiliyeti nokta atışı bir sonuca ulaşmak tam da gereken şeydir ve sonuçtan sapma olasılığını ortadan kaldırır.
● Kapasite. UWP'ler, strand pelletizerler için 20.000 kg/saat ve su halkalı pelletizerler için 5.000 kg/saat'e karşılık 30.000kg/saate kadar çıktı kapasiteleri için tasarlanabilir.
● Çok yönlülük. UWP, geniş parametre kontrol spektrumu sayesinde hemen hemen her polimeri işleyebilir. Compounding, hotmelt, masterbatch, polimerizasyon ve geri dönüşüm de dahil olmak üzere tüm uygulamalar için kullanılabilir. Hotmelt hariç tüm bu uygulamalar için strand pelletizerler kullanılabilir. Su halkalı pelletizerler, daha düşük üretim kapasiteleri ve yüksek erime mukavemetli malzemelerle sınırlandırmaları nedeniyle, geri dönüşüm ve geri kazanım için başlıca tercih nedenleridir .
● Bıçak ömrü. Kesicinin kalıp yüzeyi üzerindeki basıncının hassas kontrolü sayesinde UWP de daha uzundur.
● Pelet çapları aralığı. Geniş çaplardan mikropelete kadar, masterbatch ve expandable polistirenden rotomolding malzemesine kadar birçok farklı tip rahatlıkla UWPde üretilebilir.
● Pelet ölçü kararlılığı ve geometrisi. UWP'lerde üretilen peletler, boyut olarak daha üniform olmanın yanı sıra, haznelere ve besleme boğazlarına akışı iyileştiren ve stok yoğunluğunu artıran küreye yakın bir şekle sahiptir.
● Toz ve çapak. Polimerin eriyik halde kesilmesi nedeniyle diğer kesim sistemlerine oranla çok daha düşük.
● Sıcak ekipman ile entegrasyon. Operatör, ekstrüdere, besleme ekipmanına, ekran değiştiriciye ve eriyik pompasına erişmek için pelletizer sistemi üzerinde tek bir arayüz kullanabilir.
● Ayak izi. Şeritli pelletizerlere kıyasla küçük.
UWP’nin dezavantajı yokmu? Elbette var. Maliyet ve karmaşıklığın yanı sıra, UWP sisteminin bir dezavantajı daha vardır: Hassas ürünler çalıştırılırken kalıptaki eriyiğin kalıbı terketmeden önce "donma" potansiyeli. Bu olay sıcak ekipmandaki herhangi bir proses varyasyonu, kalıp plakasının aşırı soğuması veya düzensiz polimer akışını gibi durumlarda ortaya çıkar. Donmanın en büyük etkisi proses kesilmesidir. Donmayı önlemek için kalıp plakasında tutarlı ve yüksek düzeyde bir eriyik basıncı ile eriyik ve kesim suyu sıcaklığının iyi ayarlanması gerekmektedir.
SU HALKALI KESİM HATTI
Su halkalı pelletizerlerde (WRP'ler), UWP'lerde olduğu gibi, erimiş polimerin yuvarlak bir kalıpta dairesel şekilde dizilmiş olan deliklerden makarna halinde çıkarken kalıp yüzeyinde sürekli ve hızla dönen bir dizi bıçak tarafından sürekli kesilmesi ile çalışır. Kalıp yüzü sertleştirilmiş özel metalden yapılmıştır, böylece aşınma esas olarak bıçaklarda meydana gelir. Kalıp yüzü ile uygun teması sağlamak için kesme tertibatına hidrolik olarak basınç uygulanır.
WRP'ler, aspirin tabletlerine benzer şekilde yuvarlak ancak düz olan peletler üretir. Polimer kalıp deliklerinden çıkarken ve dönen bıçaklar tarafından kesilirken, elde edilen granüllerr, kesme odasına teğetsel olarak beslenen yüksek debili ve hızlı bir su halkası tarafından taşınır. Su, düşük olan sıcaklığı itibariyle peletleri soğutur, birbirlerine yapışmasını engeller. Granüllerin daha önce açıklanan şekilde çalışan bir santrifüjlü kurutucuya girişi taşınması için su bir oluk vasıtasıyla ilerlediği yok boyunca soğutmaya devam eder. Su, yine kurutucu girişinde granüllerden ayrılır ve bir filtreleme sisteminden geçirilerek tekrar kesici içine geri pompalanır.
WRP, üç ana pelletizer işleminin en kompakt olanıdır ve bir dereceye kadar otomasyon sağlar. Bir operatör, sistemi durdurmak ve başlatmak için bir düğme kontrolünü kullanarak ve pelet boyutunu kontrol etmek için kesicinin dönme hızını ayarlayarak sistemi kolayca kontrol edebilir. Sistemin maliyeti UWP ye göre daha düşüktür. Kalıbın diğer tarafında yine su olmasına rağmen basınçlı suyla dolu kapalı bir hazne olmasığı için eriyik sıcaklığı ve basıncı gibi sıcak proses varyasyonlarına karşı önemli ölçüde daha az hassastır ve kalıp donması sorunları oluşturmaz.
Peletler erimiş polimerden soğutma suyuyla karşılaşmadan hemen önce kesildiğinden, WRP esas olarak poliolefinler ve polistiren gibi yüksek erime mukavemetli malzemelerin işlenmesiyle sınırlıdır. İşlem, özellikle yüksek ısı veya yapışkan malzemeler için uygun değildir. UWP'lere kıyasla kapasite sınırlamaları da vardır.
STRAND KESİM HATTI
Strand pelletizerde polimer şerit (bu şekle birçok benzetme yapılabilir, makarna, tel, kablo, şerit veya yuvarlak profil gibi, ki biz bu makalede şerit olarak adlandıracağız) şeklinde üretilir. Bu sistem doğası gereği ekstrüzyon boru-profil prensibine göre çalışır. Erimiş polimer, malzemenin kalıptan her biri bir polimer şeridi oluşturan çok sayıda delikten çıkar ve bir su banyosuna daldırılır, burada soğutulur, katılaştırılır, daha sonra bir banyodan çıkarılır ve hava bıçağı ile kurutulur. Son olarak küçük silindirik parçacıklar halinde doğranır. Bu formun bir dezavantajı, silindirlerin düz uçlarının birbirine yapışabilmesi ve köprülemeye neden olabilmesidir.
Kesildikten sonra, granüller, büyük boyutlu topakları veya aglomerleri ayıklayan ızgara tipi bir ayırıcıya düşer.
Düşük maliyetli olmasının yanı sıra, şerit pelletizer çok çeşitli polimerlerle kullanılabilir, diğer pelletizer sistemlerine göre kullanımı daha basittir, temizlik ve renk değişiklikleri için bileşen yüzeylerine daha kolay erişim sağlar ve hızlı değiştirme yoluyla polimer değişimlerini kolaylaştırır. Bu nedenle, küçük ölçekli ısmarlama reçete üretimi yapan ve sık malzeme değişitiren şirketler için uygundur.
Şerit pelletizer otomasyon için çok az olanak vaad eder ve diğer pelletizer sistemlerine göre daha fazla manuel iş gücü gerektirir. Örneğin, her yeni iş başlangıcında kılavuz rulolarının altından ve üstünden 75 şeride kadar ipin çekilmesiyle ilgili işi düşünün. Bu tip pelletizerler ayrıca, bazı uygulamalarda gerekli olan küçük peletlerin şerit kırılmadan elde edilmesi zor olduğundan, yapılabilirliği granülün boyutu ile sınırlıdır. Belli bir ölçeğin altında üretilemez. Diğer iki zayıf nokta, şeritlerin katılaşma sonrasında kesilmesinden kaynaklanmaktadır. Diğer pelletizer sistemlerine kıyasla kesici aşınması ve toz ve ince tanecik oluşumu için daha büyük bir potansiyel vardır. Ayrıca, şeritlerin kopmasına, düşmesine, sarmasına, havuzda birikmesine ve diğer zorluklara neden olabilen proses değişikliklerinden ve çevresel faktörlerden daha kolay etkilenir. Ve son olarak, bir su banyosu ihtiyacı, strand pelletizerlerin fabrika zemininde daha büyük bir alanı kapladığı anlamına gelir.
Bu "kuru kesim" işleminin bu zayıflıklarından bazıları, alternatif bir yağmurlama sistemi ve "ıslak kesim" ile hafifletilebilir. Bir su banyosu yerine, teller bir su kaydırağına girer, burada püskürtülen su ile şeritler soğutur ve şeritleri kesiciye doğru hareket ettiren kademeli bir su akışı sağlanır. Bu sistem, bir hava bıçağı kullanmak yerine, işlem suyunu kesiciden hemen önce şeritlerden ayırıp nispeten daha yumuşak olan kesimin ardından su ve kesilmiş granülleri tekrar birleştirerek daha fazla soğutma sağlar. Peletleri taşıyan su, ünitenin altındaki bir santrifüjlü kurutucuya girer ve aynı prensipte pelletler kurutulur.
Su kaydırağı sisteminde, şeritler hala ıslak ve su banyosu sistemine göre daha yumuşak bir safhada kesildiğinden, daha az kesici aşınması olur. Su kaydırağı sistemi ayrıca proses suyu koşulları üzerinde daha fazla kontrol sağlayarak otomasyon için daha fazla kapsam sağlar. Buna ek olarak, "kendi kendine sarma" özelliği vardır, bu sayede düşen şeritler, su kaydırağına beslenirken değiştirilir ve operatör müdahalesi ihtiyacını azaltır. Öte yandan, kurutma işlemi, işlem suyu sisteminde daha karmaşık bir filtreleme tekniği gerektiren ek toz ve ince taneler üretir. Bu, su halkalı ve su altı pelletizerlerle birlikte kullanılan santrifüjlü pelet kurutucular için de geçerlidir.
PELLETIZER SEÇİMİNİ ETKİLEYEN FAKTÖRLER
Başlıca pelletizer sistem türlerinin yetenekleri ve gereksinimleri hakkındaki bu çalışma, her uygulama için pelletizer alternatiflerinin en ideal olanlardan olmayanlara kadar değiştiğini açıkça ortaya koymaktadır. Sistem türleri arasındaki farklar, yukarıdaki içerikte özetlenmiştir.
Tablo 1'de gösterildiği gibi, mevcut sistemlerde üretilen peletler şekil, tutarlılık, akış özellikleri ve toz ve ince tane oluşumu açısından büyük farklılıklar gösterir. Bu özellikler, bir sonraki işleme sistemlerinde pelet performansını önemli ölçüde etkiler.
Tablo 2'deki üretim faktörlerinin karşılaştırılması, mevcut pelletizer sistemleri arasında daha da büyük farklılıklar göstermektedir. Başlıca farklılıklar arasında sermaye yatırımı, çıktı kapasitesi, otomasyon kapsamı ve dağıtım esnekliği yer alır. Bir sistemin yüksek hacimli bir polimerizasyon tesisi, özel bir bileşik oluşturucu veya sınırlı bir bütçeye ve sistem karmaşıklığı için düşük toleransa sahip bir şirket içi bileşik oluşturucu için doğru olup olmadığını belirlerler.
Pelletizerler ayrıca Tablo 3'te gösterildiği gibi etkili bir şekilde işleyebildikleri polimer türlerinde de büyük farklılıklar gösterir. Sadece tek bir sistem, su altı pelletizer, hemen hemen her tür polimeri işleyebilir.
Pazarda tartışılan tüm sistemler için yeterince kullanım alanı var. Plastik ürünlerin tüketimindeki güçlü küresel büyüme, gelişen bir geri dönüşüm endüstrisi ve yerel reçine, bileşik ve katkı maddesi üretimine yönelik bir toplama eğilimi nedeniyle pelletizer sistemleri için büyük bir potansiyel bulunmaktadır. Bu talebi karşılamak için, pelletizer sistemi tedarikçilerinin iyileştirilmiş ve yenilikçi ekipman geliştirmeleri konusunda güvenilebilir.
Nordson BKG pelletizer sistemleri için lütfen bize ulaşın.
Bu makale, yazar Merritt H. Christian'ın (Nordson Corp) Plastics Technology Ekstrüzyon 2018 Konferansında verdiği bir sunumdan uyarlanmıştır.