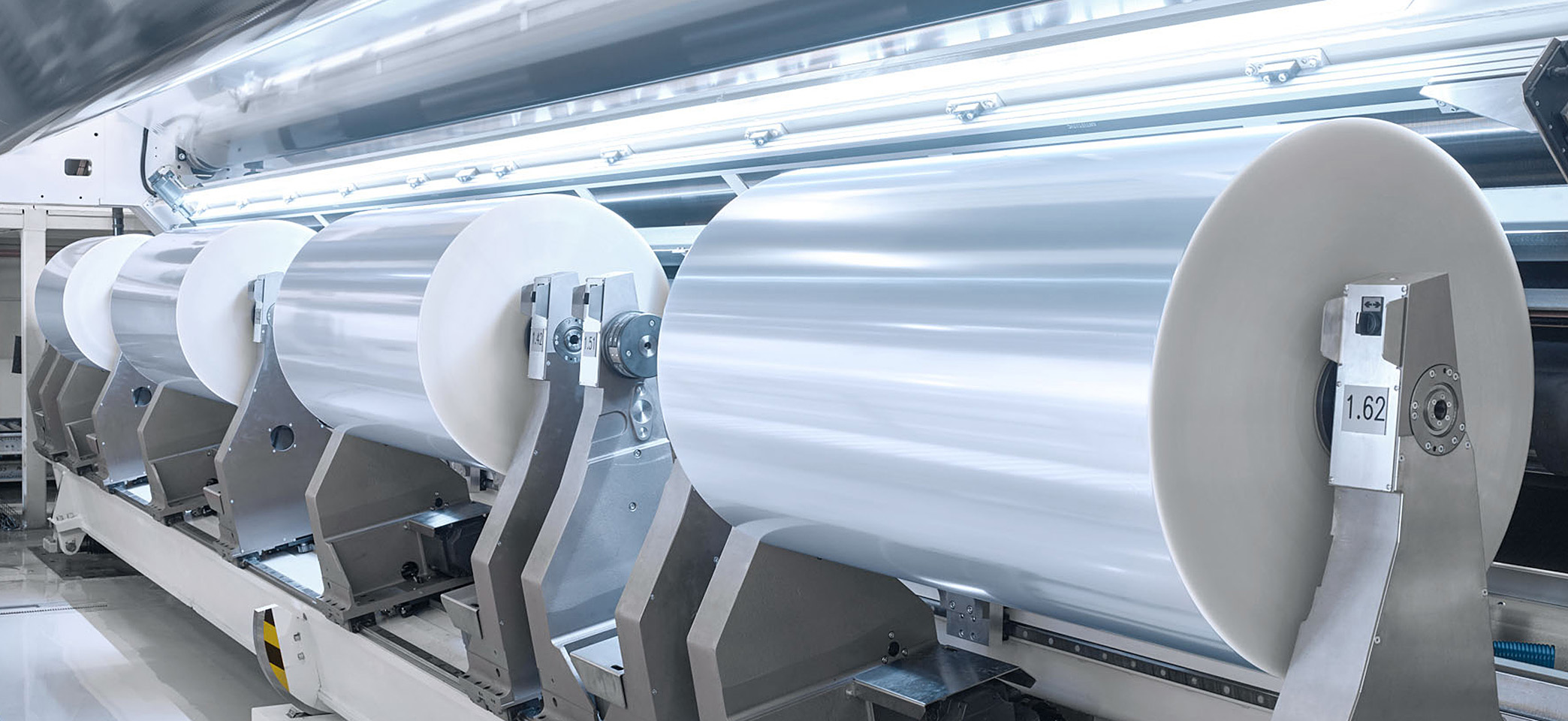
Film Ekstrüzyonunda Jel - Bölüm3
Ekstrüzyonda Jel ile Başa Çıkma Stratejileri
Şekil 1
Gerçekte, büyük bir öncü jel sorunu olmadığı sürece, oksitlenmiş jellerin kabul edilemez bir büyüklüğe ulaşacak kadar büyük ve çok sayıda olması zaman alacaktır. Bu slaytta, aynı ekstrüder üzerinde, aynı çıkışta, ancak farklı erime sıcaklıkları kullanarak aynı polimer grubunu çalıştırdığımızı varsayıyoruz.
Şekil 1'deki grafik, farklı erime sıcaklıkları göz önüne alındığında zaman içinde jellerin seviyesini göstermektedir.
1. durumunda ekstrüdere 220 derecelik bir erime sıcaklığıyla başlıyoruz ve jel seviyesinde hafif bir artıştan sonra eğrinin seviye atladığını gözlemliyoruz.
2. durumunda erime sıcaklığını birkaç derece arttırırız ve kabul edilemez jel seviyesine ulaşılana kadar jel seviyesinin yavaşça arttığını buluruz.
3. durumunda, daha fazla erime sıcaklığı artışı ile, kabul edilemez jel seviyesine daha da erken ulaşılır.
3x saat olarak işaretlenmiş eğrideki nokta 1 ila 9 saat arasında her şeyi temsil edebilir. Bu nedenle x saat 20 dakikadan 3 saate kadar herhangi bir şey olabilir. Kabul edilemez jel seviyesine ulaşmak için gereken süre, sadece erime sıcaklığına değil, aynı zamanda ekstrüderin içinde kalma süresini ve shear oranını belirleyen ekipman ve proses ayarlarına da bağlıdır.
Şimdi bu eğrilerin gerçek şeklinin bazı nedenlerini tartışmaya çalışalım. Oksitlenmiş moleküller büyüdükçe, genellikle (akış kanalının daha çok statik ve nispeten düşük shear oranına sahip bölgelerinde) metal yüzeylere tutunurlar ve metale yapışabildikleri sürece daha da büyürler. Bu moleküller, eriyik akışı tarafından sürüklenecek boyuta ulaşana kadar yavaşça büyüyecektir. Metal yüzeylerde moleküler büyüme ve ekstrüderin dışına taşınma süreci sürekli olarak gerçekleşir. Ekstrüder ilk çalıştırıldığında, bu moleküllerin boyutu metal yüzeylerden uzaklaştırılamayacak kadar küçüktür ve bu nedenle jel seviyesi düşük olacaktır. Zaman içinde boyutları büyüdükçe metal yüzeyden ayrılıp eriyik içinde taşınan miktar da artar. Bir noktada eriyik içindeki jel seviyesi bir dengeye varır. Bu seviye kabul edilebilir seviyenin üzerindeyse sorun var demektir.
Jellerin filmde mevcut olduğu, makine yönünü gösteren bir çizginin içinde toplandığı sıklıkla gözlenir. Bu genellikle, kafa içinde ve filtre alanında büyük partiküllerin daha küçük parçalara parçalara ayrılması olarak tariflenebilir.
Ekstrüzyon sırasında jellerin oluşmasına neden olabilecek faktörleri tartışmadan önce bunları aşağıdaki gibi özetleyebiliriz.
- 1) Vida tasarımı
- 2) Vida üzerinde aşınma
- 3) Kalıp ve ekstrüder içindeki ölü noktalar
- (Bu 3 faktör esas olarak polimer moleküllerinin ekstrüderin içinde geçireceği zaman ile ilgilidir, ekstrüderde kalma – ikamet süresi olarak adlandırılır)
- 4) Kapatma ve başlatma prosedürleri
- 5) Yüksek shear
- 6) Geri dönüşüm malzeme (regrind) kullanımı
- 7) Sıcaklık kontrolü / profil ekstrüder
- 8) Üretim çalıştırma sırası
- 9) Tedarikçiden taşınan öncü jeller
Şekil 2
Bahsedilen ilk 3 faktörü tartışmak için Ortalama İkamet Süresi (residence time) ve İkamet Süresi Dağılımının (RTD) ne anlama geldiğini anlamamız gerekir. Sadece polimer çalıştıran bir ekstrüderi ele alırsak, kalıptan çıkan açık bir eriyik görmemiz gerekir. Polimer molekülünün ekstrüder içinde ortalama ne kadar zaman geçirdiği hakkında bir fikir edinmek için (Ortalama İkamet Süresi) bir avuç pigment kullanarak basit bir deney yapabiliriz. Pigment besleme bölümünden ekstrüdere bırakılır ve kalıptan çıkan pigmentin yoğunluğu (veya ağırlığı) izlenerek, ekstrüderde hareket eden farklı moleküller için zaman içinde alınan dağılım hakkında bir fikir edinilebilir. Yukarıdaki grafikte, iki dakikadan biraz daha az bir zamanda mavi pigmentlerin yoğunluğu görülmektedir. Miktar önce artar, maksimum yoğunluğa ulaşır ve tekrar azalmaya başlar, bir süre sonra da tamamen yok olması beklenir. Grafikteki mavi alanın taban genişliği “İkamet Süresi Dağılımıdır”, dikey çizgi ise moleküllerin “Ortalama İkamet Süresini” gösterir. İlk mavinin görünür hale geldiği an ile son mavinin kaybolduğu zaman arasındaki zaman farkı ne kadar büyük olursa, İkamet Süresi Dağılımı'nın "genişliğinin" o kadar büyük olduğu söylenir. Bu dağılım ne kadar geniş olursa jel oluşumunda o kadar çok sorun bekleyebileceğimizi söyleyebiliriz.
1) Vida Tasarımı
LDPE Güney Afrika pazarına girdiğinde Arşimet vidası çok popüler bir tasarımdı. Bu tasarım, besleme bölümünden erime bölümüne ve son olarak ölçüm bölümüne geçerken sürekli yükselen bir çekirdek çapından (konik) oluşur. Bu vida içinde helezon adımları sabit kalır. Bu tasarımın en büyük dezavantajı, çekirdek çapının maksimum olduğu kısımda uyguladığı yüksek shear oranıdır. LDPE genellikle bu alandaki shear ve sıcaklık artışlarını kaldırabilir ancak bunu başaramadığında, malzeme bozunmaya ve jel formasyonu oluşturmaya başlar.
Bunun bir sonucu olarak, GPDP vidası gibi tasarımlar, hem LDPE hem de LLDPE'yi çalıştırma yeteneğinin gerekli olduğu bir optimal dizayn haline gelmiştir. GPDP vida, sabit bir çekirdek çapına sahip olduğundan polimerde çok daha az shear meydana gelir ve sıkıştırma dozajlamadan hemen önce helezon adımlarınn azalması ile oluşturulur.
Bariyer vidaları ileri düzey tasımlara sahiplerdir. Tipik olarak belirli karışımlar ve polimerlerin için tasarlanmıştır. Polimer olarak önemli miktarlarda LDPE kullanıldığında, bozunma ve jel oluşumunun engellenmesi için bariyer tip vida tasarımlarının kullanılmasını gerekebilir.
Ekstrüzyonda altın kural, makinenizde ne tür bir vidaya sahip olduğunuzu ve hangi karışım kombinasyonu / karışım oranı için tasarlandığını bilmektir.
Şekil 3
2) Vida Aşınması
İyi durumda bir ekstrüderimiz olduğunu ve sürekli sabit bir çıktı miktarı ile çalıştığımızı varsayalım. Siyah eğri, bu örnek için polimer moleküllerinin ikamet süresi dağılımını temsil eder. Zamanla, sürtünme sonucu vidalar aşınmaya başlayacaktır. Bu, vidanın helezon kanatları ile kovan arasındaki boşluğun artacağı anlamına gelir. Bu değişiklik polimer eriyiğin daha fazla geri akışına neden olacaktır. Çıktı miktarını sabit tutmak için operatör yavaş yavaş ve zamanla vida hızını artıracaktır. Daha yüksek bir vida hızı, yüksek shear bölgelerindeki eriyiğe daha fazla incelmeye (daha düşük eriyik viskozitesi) neden olur ve bu da vidanın kanatları üzerinden
daha fazla geri akış demektir. Bazı polimer molekülleri artık ekstrüderin içinde öncesine göre önemli ölçüde daha uzun süre kalabilir. (Daha yüksek vida hızı, geri akışta yer almayan bazı moleküllerin öncekinden daha hızlı bir şekilde kalıptan çıkarılacağı anlamına gelir. Bu, eğrinin sol tarafının da dışa kaymasıyla sonuçlanır.) Şimdi, siyah eğriye kıyasla önemli ölçüde daha geniş bir ikamet süresi dağılımına sahip olan kırmızı eğriye sahip oluyoruz. Bu eğrinin sağ tarafı jel problemimizin kaynağıdır.
Grafikteki dikey çizgi, bu makine için belirli polimer ile mevcut ekstrüzyon koşulları altında jel oluşumu için gereken kritik zamanı temsil eder. Dikey çizginin sağında polimer moleküllerinin bir kısmının artık ekstrüderin içinde jel oluşturacak kadar uzun süre kaldığını görebiliriz.
Şekil 4
3) Kalıp ve Ekstrüderde Ölü Noktalar
Ölü noktalar, ekstrüderin içinde durgun veya yavaş hareket eden eriyik akışının bulunduğu alanlardır. Bu alanlar ekstrüder tasarımından veya metal yüzeyine yapışan tabakalaşmış polimerden dolayı ortaya çıkabilir. Kalıp tarafında ise tasarım sıklıkla bu sorunun birinci nedenidir.
Ölü noktalar, grafiğin sağ tarafına bir kuyruk ekleyerek ikamet süresi dağılımını uzatır. Ekstrüder içinde daha uzun süre kalan polimer miktarı bir önceki grafiğe göre daha az olmasına rağmen, zamanın uzunluğu belirleyicidir. Oksitlenmiş jelin çekirdeğinin rengi, molekülün ekstrüderin içinde ne kadar zaman geçirdiğinin bir göstergesi olarak kullanılabilir. Artan zamanla birlikte renk şeffaftan sarıya, sonra kahverengiye ve en son siyaha dönecektir.
Polimerin ekstrüderin içinde çok uzun süre kalması sorunuyla nasıl başa çıkabiliriz?
- Sıcaklık profili ayarlarını azaltarak radikallerin oluşumunu geciktirebilir ve jellerin oluşmasına imkan verecek süreyi artırabiliriz.
- Vidanın yenilenmesiyle (belirli sınırlar içinde) vida kanatları üzerindeki polimerin geri akışı azalır ve ikamet süresi dağılımı daralır.
- Çalışmakta olan polimer veya karışım için vida tasarımı optimize edilerek, yüksek shear bölgelerinin bir sonucu olarak ortaya çıkan aşırı sıcaklık noktaların sayısı en aza indirilebilir. Örneğin, yükselen çekirdek çapına sahip bir vidada (konik) sabit bir helezon adımı ölçüsü yerine azalan bir adım ölçüsü jel seviyelerinde önemli bir iyileşmeyi beraberinde getirebilir.
- Proses yardımcı ajanları, bir ekstrüderin içindeki tüm metal yüzeyleri bir polar polimer tabakasıyla kaplayarak kayganlaştırır. Bu katman, kovan ve eriyik arasındaki sürtünmeyi azaltarak eriyiğin akış profilini iyileştirir. Kovandaki daha polar yüzey ve daha düşük shear kombinasyonu, polimerin yüzeye yapışmasını ve ardından jel oluşumunu önler.
Startup prosedürü, yüksek shear ile başa çıkmanın yolları, geri dönüşüm malzeme kullanımı, ideal proses parametreleri, öncü jel oluşumu, shear-vizkozite eğrisi, jel tarama, jeli ortadan akldırma kılavuzu ve daha fazlası….
Bu yazının devamı için lütfen bizimle irtibata geçin…!